APL Logistics has core value-added warehousing service capabilities in manufacturing support, vendor managed inventory (VMI), kitting, sequencing, light assembly, packaging, labeling and client services. It couples these with its international and domestic transportation management operations to provide customers with an integrated, end-to-end supply chain management solutions offering.
To support its contract logistics operations, APL Logistics utilizes a suite of warehouse management systems (WMS), including Manhattan Associates “WMi/PkMS,” Dematic/HK Systems “HKwm,” and its proprietary “WMSp.” Each WMS integrates with clients’ enterprise resource planning (ERP) systems as well as with the company’s suite of transportation management systems: “OTM” Oracle Transportation Manager, “TM400” and “LoadTech.” APL Logistics’ technology solutions include systems for labor management, yard management, shipment optimization, and supply chain visibility to facilitate full order-to-delivery supply chain optimization and tracking. Integration with client’s SAP ERP systems is a core competency. Most of APL Logistics’ warehousing operations utilize radio frequency (RF) devices integrated with the warehouse management system(s) for paperless put away, picking and overall inventory management. RFID, voice data collection, integrated parcel manifesting and automated material handling solutions are also deployed when needed. In addition to APL Logistics’ suite of logistics management applications, it has also deployed a comprehensive Executive Dashboard. This dashboard provides its management team with a comprehensive view on business and how it’s performing – inclusive of financial, operational, safety, service, and other key metrics necessary to properly manage business.
APL Logistics invests significant resources in Lean Management and ongoing continuous improvement initiatives. It has a company-wide formal continuous improvement process which incorporates Lean and Six Sigma methodologies. Many of the efforts work towards reducing operational waste, streamlining operations, and standardizing its leading operational procedures and processes across its global network. According to APL Logistics, its continuous improvement efforts generated over $24 million in annual cost savings/benefits.
APL Logistics’ staff dedicated to contract logistics services numbers over 500 in five warehouses encompassing more than 1.8M square feet in Southern California. On our visit, we had the opportunity to tour three of the five different warehousing operations. They are detailed in the sections below.
Rancho Cucamonga, CA Multi-client Warehouse
APL Logistics runs a 443,190 square foot, multi-client warehousing operation in Rancho Cucamonga, CA approximately 60 miles northeast of the port of Long Beach. The warehouse has a staff of 65, working six days a week, in a two-shift operation. This facility supports a wide range of commodities, including giftware, consumer goods, electronics, and footwear.
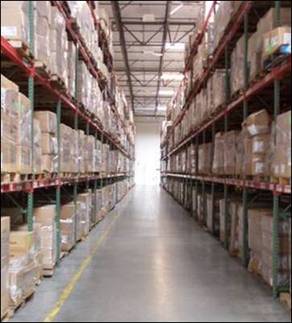
Racked Storage
As a multi-client operation, the Rancho Cucamonga facility has provided customers with significant cost savings over dedicated warehouses through reduced space, overhead, personnel and more efficient processes.
APL Logistics provides a wide-range of contract logistics services from this facility, all supported by its proprietary WMSp warehouse management system, which is able to integrate directly with customer systems. Each day, orders drop into the WMS from clients for picking and fulfillment.
The majority of inbound product is received as loose, floor-loaded cases shipped in ocean containers from Asia. APL Logistics performs inbound, quality-control checks during receiving and prior to shipping. Product storage locations are replenished using random put-away methodology. Products in this facility are stored in bulk, single racking, or two-deep racking and are slotted based upon demand in a typical “ABC” inventory management strategy with fastest movers being positioned in bulk or single rack storage locations closest to the shipping doors. Pallet and full-case, picked items are further processed in an outbound labeling and shipping area. The largest customer operation in the building is running at 99.8% inventory accuracy, 99.5% on-time receiving, and 99.5% on-time shipping.
Other services provided at this facility include order fulfillment, kit building, and returns management.
Rancho Cucamonga, CA – Dedicated Warehouse
This facility is dedicated to single client that has maintained a 22-year long relationship with APL Logistics. Today, APL Logistics manages four warehouses totaling 1.8M square feet for this customer. The four warehousing operations processed close to 100,000 orders in 2010 and had an order accuracy of 99.98%. Overall inventory accuracy was at 99.99%. In addition to inventory management and order fulfillment, APL Logistics also builds retail displays for this client as a value-added service.
APL Logistics established the 441,970 square foot Rancho Cucamonga, CA warehousing operation in 1993. The three-shift, six-day a week operation is a case picking intensive operation handling a variety of oral, personal and home care products held in on-hand inventory and positioned according to product type and order demand throughout the warehouse. The operation uses a combination of bulk floor storage for fast moving product and rack storage for medium and slower moving products.
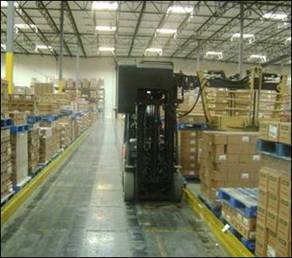
Double wide layer picking line
To manage the operation, APL Logistics is using its HKwm WMS integrated to the customer’s SAP ERP system. The WMS connects with warehouse personnel via RF scanners to drive all operational tasks from receiving through shipping.
Forty-five percent of warehouse picking is case pick and of that, approximately 55% is layer picked from four layer-picking lines. The operation’s 210 fastest moving stock keeping units (SKUs) of product are picked in the layer-picking lines; two of the lines are for soap products and two are for personal care products. Approximately 1,600 cases of product can be picked per hour using the layer-picking lines.
In 2010, the operation had 100% inventory accuracy and 99.99% order accuracy. In addition, APL Logistics implemented and completed nine continuous improvement projects in 2011 driving further productivity gains and additional costs savings for the client.
City of Industry, CA Multi-client Warehouse
APL Logistics’ 400,000 square foot, City of Industry, CA, warehouse has an approximate staff of 100 working in a single shift.
In a 120,000 square foot hi-tech customer operation, APL Logistics is processing outbound orders and return shipments. Inbound product arrives on ocean containers. All products are staged and APL Logistics performs a double-blind count against the shipment packing slips to ensure accurate receiving quantities. Individual product serial numbers and ID numbers are captured in APL Logistics’ WMS prior to being directed to put-away locations. APL Logistics is also performing location cycle counts on an ongoing basis to ensure inventory accuracy which is currently running at 99.97%. APL Logistics is processing a high volume of returned units per day. Returns processing includes receiving products, matching products to returns authorizations, determining each product’s disposition, and processing the products to be returned to the original equipment manufacturers for testing and repair.
On a project basis, APL Logistics is performing a significant array for value-added services, including product labeling, packaging, and firmware upgrades.
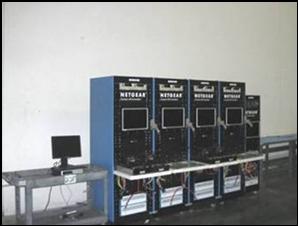
Networking equipment testing stations
In October, APL Logistics will begin testing returns of networking products and has built out multiple test stations. It will perform functional tests, firmware updates, and cosmetic checks. After the tests and programming are performed, product that can be returned to sellable inventory will be packed out and received back into the warehouse.
Daily, high volumes of individual units are shipped. The operation has a 48-hour SLA (service-level agreement) specifying that products must be shipped within 48 hours of order receipt. The operation is running at 100% on-time shipping accuracy.
Another 100,000 square feet of the warehouse is dedicated to an athletic footwear manufacturer. Shoes manufactured in Asia are received by APL Logistics and deconsolidated. The shoes are then either transloaded onto outbound trailers, intermodal containers, or put away into on-hand inventory. Picking is by zone and fairly automated using a pick-to-conveyer approach. APL Logistics builds cases by shoe sizes and performs a 100% quantity and size audit. Over half of the outbound shoe orders are destined to major retail department stores.
In addition to transloading, inventory management, and outbound order fulfillment,
APL Logistics is also performing multiple value-added services. On the day of our visit, approximately 10 people were relabeling pairs of shoes. In terms of performance, APL Logistics is currently meeting all established key performance indicators, running at 100% cycle count accuracy, 100% on-time receiving, 99.9% on-time shipping and has 100% order fill rate.
Summary
APL Logistics has a competitively differentiated service offering with the key U.S., Latin America, and Asian operations needed to support intensifying global trade. It is leveraging its global contract logistics and international transportation management capabilities in developing new 3PL business. Through its ongoing emphasis on Six Sigma and Lean process improvements, we anticipate APL Logistics will become an increasingly visible 3PL in today’s marketplace.